Industrial marking
Established since 2000, Technomark has become the fastest-growing OEM of industrial traceability solutions in the permanent marking industry. We provide dot peen and laser marking systems that increase productivity and lower total operating costs, providing manufacturers with a competitive edge in the global marketplace.
Ask us about:
- Laser marking systems
- Dot peen marking systems
- Fume extraction equipment
- 2D bar code readers
- Traceability
- Process automation
- Direct part marking (DPM)
- Training, service, and repair
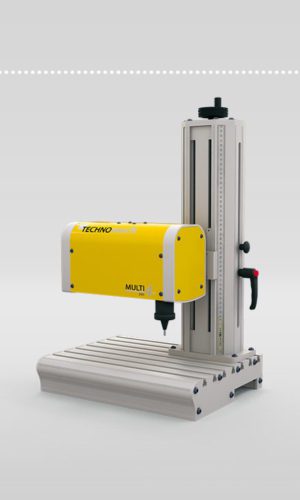
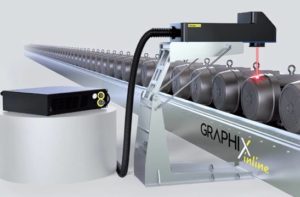
Dot Peen & Laser Marking
Component traceability throughout the product life cycle is not only good quality policy, it has become a requirement for doing business in many key industries.
Technomark has helped globally recognized companies realize the benefits of adopting a quality standard for DPM traceability, including:
- Cost containment
- Quality control
- WIP tracking in the manufacturing process
- Improved visibility across the extended supply chain
- Part authenticity
- Error-proofing of the assembly process
- Warranty management
Technomark’s industrial marking equipment helps companies satisfy quality requirements for unit-level industrial traceability of durable manufactured goods. Learn more about our core technologies for DPM:
Meeting Traceability Requirements for Your Industry
Technomark is a supplier of DPM technology across a spectrum of industries where tracking of mission-critical and high-value components is crucial to quality. Product traceability applications by industry segment include:
- Automotive: Traceability for powertrain, braking systems, fuel systems, and chassis components
- Aerospace: Part marking systems for turbines, fan blades, fuel systems, and airframes
- Medical device: Direct part marking of medical implants, surgical instruments, and OR equipment
- Electronics: Semiconductor, circuit board, and passive component marking
- Oil & gas: Down-hole tools, surface equipment
- Military & defense: Tactical vehicles, guidance systems, firearms, ballistic missiles
- Metalworking & fabrication: Precision-machined components and stampings
All links in the supply chain should work together to facilitate seamless transactions between trading partners. Technomark’s core technology helps manufacturers meet industry standards for direct part marking and traceability:
- Automotive: AIAG B-17 traceability requirements
- Aerospace: Spec 2000 part marking standards
- Military & defense: UID (Unique Item Identification)
- Medical device: UDI (Unique Device Identification)
- Oil & gas: API Spec Q1
Technomark’s factory is ISO 9001:2015-certified, ensuring quality control at every stage of the manufacturing process while promoting continuous product improvement.
Reduce Your Total Cost of Ownership (TCO)
There are many OEMs of industrial marking machinery that can supply your company with a piece of equipment at a low cost. At TECHNOMARK, our unique value proposition is that we lower your total cost of ownership over the useful lifetime of your investment. From pre-sales consultation and application development, to on-site implementation and training assistance, to ongoing technical support – TECHNOMARK lowers your TCO at each stage of the product ownership experience.