Direct Part Marking Methods: What, Why, Where & How
When it comes to direct part marking methods, there are a variety of methods available, based on the depth of the mark you need, the material you need to be marked, and the purpose of the mark.
Here we take a deep dive into the methods available, the benefits of the more widely used, and the materials to be marked. We also take a look at why and how products need to be marked.
In A Hurry? Take this resource with you!
Part Marking Methods
When it comes to dpm, or direct part marking, some of the most well-known methods include:
- Dot peen marking
- Laser marking
- Inkjet marking
- Impact presses
- Chemical etching
Dot Peen Marking
Dot peen is a direct part marking method, meaning that the marking head of the machine interacts directly with the component to achieve a permanent mark that is able to survive harsh operating environments
Dot peen machines use an impact stylus to create small indents on a part’s surface to create letters, numbers, logos, or 2D datamatrix codes. Because the mark is formed via material displacement instead of material removal, it is considered a low-stress marking technique ideal for aerospace as well as oil and gas applications.
Laser Marking
Laser marking is one of the most widely used direct part marking methods for manufacturing because of its versatility. The mark is achieved by super-heating the part surface to etch, ablate, or anneal the material substrate Target applications that are ideal for laser marking include:
- Wide range of plastics
- Ferrous and non-ferrous metals
- Elastomer compounds
- Organic materials (like wood or cardstock)
Inkjet Marking
While dot peen and laser marking systems provide a permanent traceability solution, inkjet marking is semi-permanent.
Inkjet marking functions a lot like a regular printing machine — using drops of ink to mark information on a substrate. It’s often regarded as one of the fastest marking methods, and is capable of marking on:
Impact Press Marking
Just like dot peen marking, an impact marking press indents a material with the desired identification information. However, the methods are different.
Whereas dot peen marking uses a series of cold-stamped dots to mark text, 2D data matrix codes, or logos into a material, the impact press uses a die to stamp the information instead.
Chemical Etching
Chemical etching takes a completely different approach to direct part marking. This method uses chemical compounds to subtract materials from the marking surface via a process of electrolysis to create the impression.
Chemical etching is essentially an accelerated form of oxidation. A stencil is soaked in an electrolyte solution and applied to the material. A low-voltage electric current is then applied to the stencil to initiate the oxidation process.
Chemical etching requires several steps to prepare the part for marking, but it’s a cost-efficient and quick process. It’s also less invasive than other marking methods, making it ideal for thin-wall parts.
Dot Peen Benefits
One of the biggest benefits of a Dot Peen Marking Machine is its ability to efficiently produce marks compared to other marking systems. Other benefits of Dot Peen machines include:
- Portability: battery-operated systems are ergonomic and perfect for smaller-scale operations or marking of large, heavy parts that cannot be transported to a fixed location for marking
- Versatility: state-of-the-art Dot Peen marking systems are modular and can start with a portable or manual marking system that can later be adapted to a fully automated production line
- Ease of use: Dot Peen machines are easy to program and do not require any advanced computing knowledge or technical training.
- Permanency: Dot Peen marking process yields a permanent, indelible mark that can withstand harsh operating environments
- Economical: Compared to other marking systems, Dot Peen systems are typically less than $10,000.
Materials to Be Marked
The material specification of your components will determine which direct part marking methods are best for your product application — it’s that simple.
To avoid undue costs, identify what kinds of materials you’ll need to mark before purchasing a traceability solution.
Organic Materials
Organic materials are fairly easy to identify, we are surrounded by them in our everyday life. Organic materials are naturally occurring compounds or products made from naturally occurring compounds that break down over time.
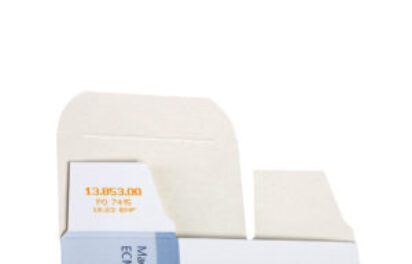
Think of materials like:
Wood | Leather | Paper | Corkboard |
Concrete | Rubber/Elastomer | Glass |
Marking on these materials can be tricky because their compositions don’t react well to direct marking techniques such as dot peen. The dot peen marking process produces a mark by displacing material at the part surface using a tool such as a carbide tip stylus. For organic compounds, this process tends to deform the material surface.
Marking on these materials can be tricky because their compositions don’t react well to direct marking techniques such as dot peen. The dot peen marking process produces a mark by displacing material at the part surface using a tool such as a carbide tip stylus. For organic compounds, this process tends to deform the material surface.
Inkjet printing is a viable option for marking organic materials for high-volume, high-speed production lines. Inkjet relies on the absorption of ink into the substrate, so it works well on wood, cardboard, paper, and corkboard. Inkjet marking is widely used in automated pharmaceutical and consumer goods packaging lines
Non-Organic Materials
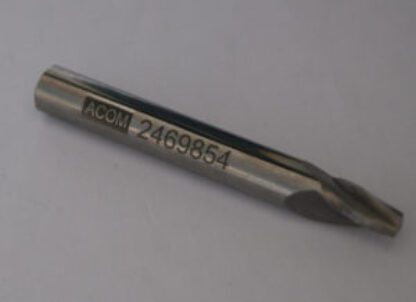
For manufacturers, this means materials like:
Steel | Titanium | Aluminum | Nickel alloys | Iron |
Powdered Metal | Brass | Copper | Polymers |
As with organic materials, many manufacturers rely on laser marking machines for the permanent identification of non-organic materials. Laser energy is focused on the material surface to achieve an indelible, high-quality mark through a process of etching, ablation, or annealing. When it comes to laser marking plastic, the laser can also produce a color change on many plastic resins through a process called foaming.
Laser Marking: Types and Benefits
Lasers for direct part marking provide a more reliable mark, sometimes without excessive waste or part impact. However, the right laser marking method might require sacrificing some of the part material to guarantee a longer life expectancy for the mark.
5 laser types
Laser part marking is common in a number of industries because it is effective for long-term part identification and meets the rigorous standards set forth for aerospace, mechanical, and other high-demand industries.
With that in mind, we can take a look at five of the commonly used lasers and the best use case for each:
1. The CO2 laser produces an infrared laser beam and uses CO2 gas as the active medium. The laser is emitted at 10.6 micrometers and features high beam quality, allowing it to focus laser power into a small spot and produce high-quality laser marks. This laser has the longest wavelength, which is located on the invisible infrared spectrum.
2. A fiber laser can also be used for embossing or to add discoloration where desired. The discoloration process with a fiber laser provides a variety of colors and better control simultaneously.
The fiber laser is the most commonly used in the laser marking industry, particularly common in aerospace, metallurgy, automotive, and mechanical applications. It’s useful for all types of metals and has a long lifespan when compared to other lasers.
3. The YAG laser operates on a wavelength similar to the fiber laser (1.064 micrometers). However, this type of laser has a different structure than a fiber laser and the beam passes through different crystals in order to create the beam.
4. The green laser is ideal for these sensitive materials because its wavelength is located near the UV spectrum generates less heat.
5. The UV laser is another subtype of the YAG laser. Thanks to implanted crystals, it became possible to adjust the wavelength for this laser and utilize others, providing access to the only laser in the invisible ultraviolet spectrum (0.355 micrometers).
Content of Part Marking:
The first question to consider is what specifically will be marked on the part. Is it:
- Text characters?
- Logos?
- Barcodes?
Most direct part marking machines are capable of marking text characters as a standard feature. However, more complex elements, such as logos or 2D barcodes, may require a software upgrade.
Another consideration is the size and density of marking. Ask yourself:
- How many characters will be marked?
- How many lines of text?
- What is the total marking area required for all elements, i.e. text, logos, and barcodes?
- Will all elements fit within the mechanical limits of the marking device itself?
Part Marking Location:
After you have answered the what, the next question is where on the part will be marked. Is the space available for marking easily accessible, or are there unique part features that restrict or obstruct access to the marking surface? Can the marking tool make physical contact with the part surface, or do you need a non-contact marking method?
Size of Part:
Understanding the item’s size dictates how (and where) the marking process occurs:
Small parts that are light enough to be hand-carried and manipulated can be presented to the marking station at a fixed location (such as an operator assembly cell).
Size of Marking:
Plainly stated: The size of the part will often determine the size of the marking itself.
Product Mix:
Will the marking machine be dedicated to a specific product, or will it be used as a general-purpose tool to mark a wide variety of parts?
A dedicated marking system can be customized to the particular needs of a given product application with minimum operator intervention required.
A production environment with a low-volume, high product mix demands a flexible marking system. Having a flexible marking system eliminates the need for dedicated tooling and minimizes operator setup time between production runs for different parts.
Production Volume:
The volume of parts to be marked within a given space or time will determine the duty cycle on the marking machine. Production rates can be defined in terms of:
- Parts per hour
- Parts per shift
- Parts per day
For low-duty cycle product applications of less than 100 parts/day, a relatively inexpensive entry-level marking machine may be adequate to satisfy production requirements. Production batches in the 100s or 1,000s of parts/day require a more robust, industrial marking machine capable of withstanding a higher duty cycle.
The level of process automation required to keep up with the desired throughput rate will also be driven by production volume. For low-volume production, an operator can feed parts manually to a stationary product loading fixture at the marking station.
Product Form and Function:
What is the intended use of the part to be marked?
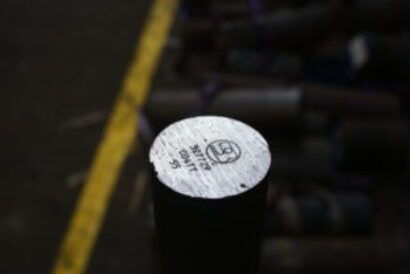
The marking process should not alter the form, fit, or function of the part itself as the part may become structurally compromised or unusable.
Controlled surfaces require a marking method that does not displace or remove material from the part surface such as laser marking. On the other hand, product surfaces that are exposed to an extreme pressure differential (such as pipe and valve fittings) call for a low-stress marking method,such as dot peen, that does not introduce thermal shock or stress fractures in the material.
Operating Environment:
Operating conditions in the production environment are an important consideration when selecting the right marking machine for the job. Ask yourself:
- will the marking equipment be used indoors or outdoors – or both?
- Is the operating environment relatively clean or will the marking machine be exposed to dust, oil spray, or liquids such as machining fluids?
- Is the production area climate controlled, or is it prone to seasonal temperature extremes?
- What is the operator’s skill level?
Budget:
While not a direct process consideration, budgetary constraints will impact which part marking technology to purchase. In the end, “the right tool for the job” often becomes “the best tool for the available budget”.
A word of caution here: many manufacturers fall into the trap of false economy by focusing solely on the initial capital outlay for the marking equipment, only to suffer higher operating costs as a result of production bottlenecks and machine downtime from a piece of machinery that is not up to the task. But why compromise?
Look for OEMs that offer equipment financing programs. Financing programs enable manufacturers to acquire the best marking technology for the job while maintaining the flexibility to pay for it over time from the operations budget rather than going through a traditional capital expenditure approval process.