Direct Part Marking 101 | Automotive Component Traceability
The number of components used to manufacture vehicles has doubled over the past decade. This means more parts to
- keep in inventory
- track during production
- evaluate throughout the life cycle to pinpoint issues
Automotive part marking requirements are intended to help with all of the above processes. This means accuracy and readability are crucial for the purpose of laser marking automotive parts, and it doesn’t hurt to have a process that makes traceability easier.
Meeting Automotive Industry Standards
The automotive industry is duty-bound to provide safe and reliable vehicles to consumers. With new models of integrated marketing equipment and technology introduced each year, it’s important to have a method of tracking parts when issues arise and a recall becomes necessary.
In recognition of the importance of recalls and safety, the automotive industry has set high standards for product identification. Automotive parts identification is required, but it also provides several benefits:
- A product can be marked with serial and part numbers, barcodes, and other information.
- Items can be tracked throughout their entire lifecycle.
- No need for traditional labels prone to fading or falling off.
- By using 2D barcodes, manufacturers can identify very small items and parts and include more data than in a linear barcode.
- Improved error prevention for just-in-sequence (JIS) production.
- Reduced risk of counterfeit parts because part marking is difficult to duplicate.
Part marking is a process used to identify automotive components, improving quality control throughout the production and life cycle of a vehicle. With vehicle components increasing and shrinking at the same time, automotive part marking becomes ever more important in order to properly track and evaluate all these components.
Traceability is also an important factor when it comes to automotive part marking, as it helps determine where each component came from and how it was made.
As such, accuracy and readability are essential for automotive part marking to be useful for the manufacturer With the right part identification methods in place, automotive manufacturers can:
- Meet industry standards
- Ensure the safety and reliability of their products
- Improve future designs
JIS production is a technique where parts are delivered to the assembly line in a manner that perfectly synchronizes with the automotive manufacturing process. Timely and precise delivery allows automotive manufacturers to make efficient use of their resources while also reducing costs. Automotive part marking plays an important role in JIS production by minimizing and ensuring production runs smoothly.
The Importance of Traceability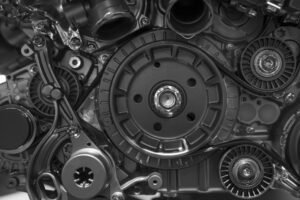
The automotive industry is relying more and more on automotive traceability requirements to ensure the quality and safety of its products. Part marking requirements are essential in helping automotive companies trace, manage, and evaluate components over the entire life cycle of a vehicle.
The implementation of direct part marking has:
- Helped with recall management
- Improved part identification on flexible assembly lines
- Improved chain of custody tracking, avoiding product diversion
Recall Management
Traceability provides an easy way to identify faulty parts. With part marking, automotive companies can identify the specific source of a faulty component, enabling them to contain and isolate problems quickly and reduce losses.
Improved Part Identification During Assembly
Automated process control systems require accurate data input for maximum efficiency, and part markings help provide that accuracy. Additionally, integrated marking equipment along the automotive production line can read and store this data to optimize the build and speed up production.
Chain of Custody Tracking Improvements
Automotive companies that use part marking are able to correctly fulfill customer requirements. Strong chain of custody tracking and the ability to avoid product diversion helps automotive companies deliver quality parts on time and keep track of what goes where in case problems arise.
Dot Peen vs. Laser Marking Automotive Parts
There are numerous methods of direct part marking that can be used for parts exposed to harsh conditions, such as vehicles that traverse a variety of terrains. Dot peen marking and laser marking are two popular methods used in the automotive industry. Both have advantages and disadvantages to consider before committing to the investment associated with your preferred method.
Dot Peen
Dot peen is a method that involves striking the metal or product material (typically metal) with a marker that knocks away a small amount of material to leave a readable mark.
Advantages of dot peen marking include:
- Lower cost.
- Durable and permanent mark
- High marking speed
- Minimal stress (mechanical only)
The disadvantages of dot peen marking include limited usefulness. In terms of materials, this method is effective for metal and plastic, but not others. The dot peen marking process also exposes parts to mechanical stress, which can weaken the component and increase the risk of part, and has the potential for increasing the occurrence of defects.
The M4 inline and automation pack can help optimize marking for automated production: https://www.technomark-inc.com/solutions/integrated-use/m4-inline/
Laser Marking
Laser marking is a non-contact method that marks parts using a precise beam. The Direct Part Marking laser has a higher rate of permanency and accuracy.
Other advantages of laser marking include:
- Permanent & accurate mark
- High-Quality mark that can be applied to many materials
- Can be done at high speeds; high contrast
- Resistant to heat and liquids
However, there are disadvantages to recognize as well. These include both higher costs for a laser marking device and issues when materials are exposed to mechanical stress. The energy cost for the laser in question depends on the type used.
Graphix Inline provides flexibility in marking depth and offers a solution for a variety of materials: https://www.technomark-inc.com/solutions/integrated-use/graphix-series-inline/
Integrating New Part-Marking Technology Into Your Process
Part coding and identification help reduce counterfeits and improve the success rates of recalls. This in turn has improved safety rates for vehicles and the ability to make the next design better.
With an ever-increasing number of parts used in vehicle manufacturing, now’s the time to audit the potential expansion of your traceability solutions. Whether you’re a contractor or handle marking in-house, and whether you prefer dot peen or laser, review the latest technology and best practices. Don’t get left behind by traceability and automotive part marking standards.
For further information on automotive applications for part marking technology, consider this resource: